Motion Analysis
For years hundreds of companies have been using Hexagon’s (MSC Software) motion analysis products, like Adams, to save money, shorten design cycles and improve their products. Companies know that motion analysis is important because product design frequently requires an understanding of how multiple moving parts interact with each other and their environment, from an automobile or aircraft to a washing machine or assembly line. Moving parts generate loads that are often difficult to predict. Complex mechanical assemblies present design challenges that require a dynamic system-level analysis to be met. Accurate modeling can require representations of various types of components, like electronic controls systems and compliant parts and connections, as well as complicated physical phenomena like vibration, friction and noise. Motion analysis enables one to meet these challenges by quickly evaluating and improving designs for important characteristics like performance, safety and comfort. Hexagon’s (MSC Software) solutions for motion analysis cover a broad range of multibody dynamics simulation functionality provided through rich, easy-to-use pre and post-processing interfaces and industry leading solvers.
Import detailed geometry from a wide variety of high-end and mid-range CAD packages as well as numerous neutral formats.


Flexible Body Representation
Represent the flexibility of model components by importing finite element models from most major FEA software packages. This will allow the capture of inertial and compliance properties which will increase load prediction accuracy. By including Hexagon’s (MSC Software) efficient modal flexible body representation for only those parts whose compliance is important to the solution accuracy simulation times are drastically shorter than those seen on FEA-only environments. Post-processing allows for visualization of individual components’ mode shapes as well as their compliance in full system animations. Contour plots of deformation and recovered stresses are also available.


Contact Modeling
An important part of many multibody systems is the contact that occurs between the parts. Hexagon’s (MSC Software) motion analysis offerings provide a variety of contact modeling functionality. Rolling and sliding contacts and impact can be represented between rigid bodies, flexible and rigid bodies as well as between two flexible bodies. Contact primitives provide a highly-efficient solution for simple geometry. More sophisticated methods are used for contact between complex geometries both rigid and flexible. In no case is a previous knowledge of “contact regions” required.


Durability Analysis
Durability issues discovered too late in the development cycle will cost you time and money. If they are not addressed before product launch they will lead to high warranty costs and low customer satisfaction. Durability testing is a critical aspect of product development. The ability to answer the question “Will it last?” can affect not only the design of a component, but the entire system. Good durability characteristics often conflict with other attributes, such as ride and handling or NVH, and finding a way to balance competing requirements is necessary. Accurately replicating durability tests is an important step on the path towards optimal design.
Hexagon’s (MSC Software) solutions allow one to assess stress, strain, or life of components in your system model. By interfacing to fatigue programs life predictions and factor-of-safety analyses are possible. Model correlation and process streamlining is enabled through direct access to physical test data in industry-standard file formats. Hexagon’s (MSC Software) products also allow one to extend the component mode synthesis capability used for flexible body integration and recover stresses on flexible bodies. Results from a motion solution are combined with modal stresses from FE to more accurately predict the stress in a flexible component. All stress or strain resulting from external forces or constraints and inertia effects can be recovered in the most efficient way.


Vibration Analysis
Perform system-level vibration analyses like frequency response studies and normal modes analysis. Hexagon (MSC Software) solutions provide vibration-specific modeling elements like frequency dependant bushings and forcing functions for power spectral density, swept-sine and rotational imbalance. Coupled with vibration and frequency-domain specific post-processing, this leads to easy analysis and visualization of system modes, frequency response, modal participation tables, component energy distribution, etc.


Control System Integration
Most physical systems are a combination of mechanical components actuated by pneumatic, hydraulic or electrical subsystems that are controlled by electronic control units. System models need to fully account for actuation and control systems effects to correctly capture the behavior of the complete assembly. Typically, control systems are best represented by block diagrams with results viewed in plots and motion models are commonly represented by three dimensional geometry with output viewed in graphical animations as well as plots. Hexagon’s (MSC Software) motion analysis offerings allow easy integration of the mechanical system and control system models. Controls-specific elements are included Hexagon (MSC Software) products. Also once can incorporate the mechanical models within block diagrams of the control system design software itself or directly import the actuators and/or controllers from the controls design software in the mechanical system simulation environment. Such interaction is supported with MATLAB/Simulink from The Math Works, Inc. and Hexagon’s (MSC Software) EASY5 software.


Design Study, DOE, and Optimization
For simple design problems, you can explore and optimize the behavior of your mechanical system using a combination of intuition, trial-and-error, and brute force. As the number of design options increase, however, these methods become ineffective in formulating answers quickly and systematically. Varying just one factor at a time does not give you information about the interactions between factors, and trying many different factor combinations can require multiple simulations that leave you with a great deal of output data to evaluate. To help remedy these time-consuming tasks, Hexagon (MSC Software) provides planning and analysis tools for running a series of experiments that helps to determine relevant data to analyze, and which automates the entire experimental design process. This helps increase the reliability of your conclusions, get you answers faster than trial-and-error or testing factors one at a time, and help you better understand and refine the performance of your mechanical system.

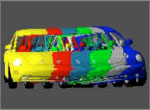
Customization and Automation
Time is saved and a broader user audience can be reached by tailoring the analysis environment for specific needs. Hexagon’s (MSC Software) motion analysis solutions provide multiple means of automating the model construction, solving, and post-processing activities. Model construction can be automated by macros or templates. Custom interfaces can be created and incorporated directly into the “off-the-shelf” tool. And, powerful industry/application-specific packages are available from Hexagon (MSC Software) and our business partners.


Request information
D2S International offers consultancy services using finite element software from HEXAGON (MSC Software).